Ensure right product data quality throughout the product development phase with Q-Checker
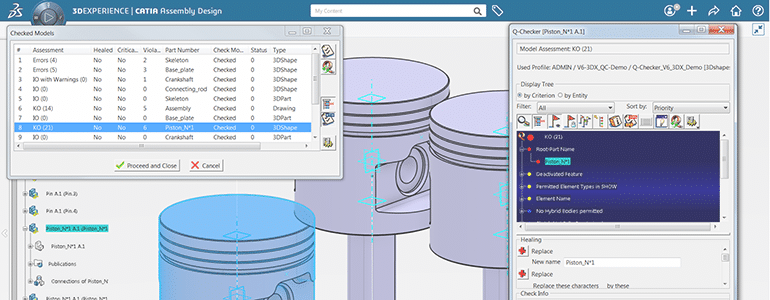
- Sushil Punaskar
- December 25, 2024
What is Product Data Quality and Why it Matters the Most
Product Data Quality: The What’s and Why’s
Product Data Quality comprises of creating, ensuring, distributing acceptable quality of CAD designs across the organisations and in upstream or downstream uses as well.e.g. Tier-1 Suppliers and or Original Equipment Manufacturers, OEMs. Correct part specifications pertaining to ensuring if material, coatings, thickness, GD&T annotations has been added to the designs or they are missed due to Human errors. Ensuring product data Quality despite of all the traditional methods like ‘Release check lists’, ‘Pre-delivery Check list’, ‘Drawing check list’, adherence to CAD standards of company is not enough and they have many drawbacks as mentioned below. The business risk arising due to bad data quality is enormous since bad data quality can significantly delay the entire product development Milestone-Releases, and as a company there must be a robust solution in place to factor this risk well in advance. CAD data either in PLM/PDM systems or in central servers is a master-print that all the stake holders in a development cycle refer-to, work-upon and rely upon. In all matters of engineering disputes, CAD data is a master that all refers to always and hence there are many organisations that count data quality as a risk factor project risks document. this clearly describes the importance of data quality.
Fig 1: list of Stake holders using product data in a typical development cycle.
Emphasising fro figure 1 how multiple stake holders has to-and-fro communications with the Product data. Any discrepancy in cad arising out from mediocre CAD modelling, missing specifications, unwanted geometries showing up, GD&T callouts and datums incorrectly specified will create these stake holders hold up their work.
Fig 2: Traditional methods to ensure product data quality (PDQ) in organisation and drawbacks of it.
Benefits of Q-checker in Product Data Quality
- Save Time Spent Fixing Models: Fixing geometry problems constitutes a significant design cost, not only in terms of time and quality, but also in wasted human and material resources. The repairs that are not made at the outset are often compounded when users of different downstream applications use different methods to “fix” the original model. With Q-Checker, critical defects can be identified and repaired before faulty features lead to additional geometric problems.
- Pro-Active Learning: The learning curve can be steep and tedious at times, particularly for new and part-time designers who need to conform to specific customer CAD standards. Q-Checker can assist by identifying common design process mistakes and inefficient practices. Like supporting each designer with the experience and advice of an expert user.
- Promotes Design Reuse: Because defects have traditionally been so common in models, most users prefer to rebuild their own, instead of reusing existing ones. This is another costly part of designing that Q-Checker can help to eliminate.
- Enforcing Internal CATIA Standards: Q-Checker helps to ensure that corporate design standards and specifications for using CATIA are adhered to, allowing the design and production teams to become more productive, efficient, thereby supporting higher product quality.
- Supplier Confidence: OEMs working with Q-Checker have the confidence that they are sending their suppliers good quality data. At the same time, they can insist that their suppliers use a specific checking profile. Suppliers who use Q-Checker can assure their customers and partners that they are delivering accurate models that are based on a consistent and disciplined CAD modelling practices.
- Check Files Transferred from Other CAD Software: CATIA users frequently need to use multiple CAD systems and data, a practice that can lead to problems with data translation. This usually calls for significant reworking and redesigning. Q-Checker helps to catch errors and adjust standards quickly and effectively, allowing for speedy recovery.
- Check Seal: Q-Checker allows users to store the model results in a check seal. This provides still greater security and helps to save time since the receiving part does not have to be rechecked against the specified Profile.
- Designer Awareness: Q-Checker anticipates and captures requirements of all downstream applications, even where they may not be evident to the designer. When operated already from the early beginning in the design process, Q-Checker will support and enhance cross-engineering as well as model reuse. The key to a successful implementation is the integration and adaptation to companies PLM processes.
Q-Checker: Interactive checking of CAD Data
Q-checker interactively checks the CAD designs i.e. parts, drawings, assemblies right in CATIA workbench and qualify immediately if the data meets the quality requirements as per company CAD standard or as mentioned in Q-checker profile. Q-checker can be run in a batch mode. There are more than 400 Data Quality checks already in-place in shipped licenses of Q-checker out of that 200+ checks have auto-healing function. Auto-healing function of Q-checker resolve the CAD concerns right automatically.
Figure 3: Q-Checker Interactive check user interface.
Q-Checker: Check Profile Creation
In any organisation, there can be many departments that have varying needs from the CAD designs. e.g. CAE team requires material specs, thickness, fixing locations etc, electrical team might not need these. So, Q-checker facilitates creating Check profiles individually for various departments in a organisation. Figure 4 showcases how to create check profiles in Q-checker and save according to the department name e.g. Electrical profile, Chassis profile, interior trims profile etc.
Fig 4: Q-Checker Profile creation UI.
We’ll discuss in detail some of the standard checks in the upcoming series.
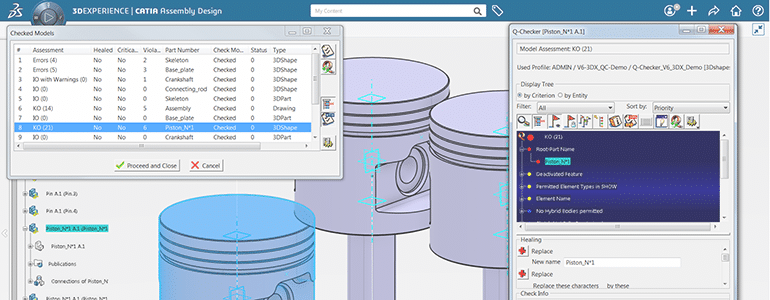
- Sushil Punaskar
- December 25, 2024
Ensure right product data quality throughout the product development phase with Q-Checker
What is Product Data Quality and Why it Matters the Most
Product Data Quality: The What’s and Why’s
Product Data Quality comprises of creating, ensuring, distributing acceptable quality of CAD designs across the organisations and in upstream or downstream uses as well.e.g. Tier-1 Suppliers and or Original Equipment Manufacturers, OEMs. Correct part specifications pertaining to ensuring if material, coatings, thickness, GD&T annotations has been added to the designs or they are missed due to Human errors. Ensuring product data Quality despite of all the traditional methods like ‘Release check lists’, ‘Pre-delivery Check list’, ‘Drawing check list’, adherence to CAD standards of company is not enough and they have many drawbacks as mentioned below. The business risk arising due to bad data quality is enormous since bad data quality can significantly delay the entire product development Milestone-Releases, and as a company there must be a robust solution in place to factor this risk well in advance. CAD data either in PLM/PDM systems or in central servers is a master-print that all the stake holders in a development cycle refer-to, work-upon and rely upon. In all matters of engineering disputes, CAD data is a master that all refers to always and hence there are many organisations that count data quality as a risk factor project risks document. this clearly describes the importance of data quality.
Fig 1: list of Stake holders using product data in a typical development cycle.
Emphasising fro figure 1 how multiple stake holders has to-and-fro communications with the Product data. Any discrepancy in cad arising out from mediocre CAD modelling, missing specifications, unwanted geometries showing up, GD&T callouts and datums incorrectly specified will create these stake holders hold up their work.
Fig 2: Traditional methods to ensure product data quality (PDQ) in organisation and drawbacks of it.
Benefits of Q-checker in Product Data Quality
- Save Time Spent Fixing Models: Fixing geometry problems constitutes a significant design cost, not only in terms of time and quality, but also in wasted human and material resources. The repairs that are not made at the outset are often compounded when users of different downstream applications use different methods to “fix” the original model. With Q-Checker, critical defects can be identified and repaired before faulty features lead to additional geometric problems.
- Pro-Active Learning: The learning curve can be steep and tedious at times, particularly for new and part-time designers who need to conform to specific customer CAD standards. Q-Checker can assist by identifying common design process mistakes and inefficient practices. Like supporting each designer with the experience and advice of an expert user.
- Promotes Design Reuse: Because defects have traditionally been so common in models, most users prefer to rebuild their own, instead of reusing existing ones. This is another costly part of designing that Q-Checker can help to eliminate.
- Enforcing Internal CATIA Standards: Q-Checker helps to ensure that corporate design standards and specifications for using CATIA are adhered to, allowing the design and production teams to become more productive, efficient, thereby supporting higher product quality.
- Supplier Confidence: OEMs working with Q-Checker have the confidence that they are sending their suppliers good quality data. At the same time, they can insist that their suppliers use a specific checking profile. Suppliers who use Q-Checker can assure their customers and partners that they are delivering accurate models that are based on a consistent and disciplined CAD modelling practices.
- Check Files Transferred from Other CAD Software: CATIA users frequently need to use multiple CAD systems and data, a practice that can lead to problems with data translation. This usually calls for significant reworking and redesigning. Q-Checker helps to catch errors and adjust standards quickly and effectively, allowing for speedy recovery.
- Check Seal: Q-Checker allows users to store the model results in a check seal. This provides still greater security and helps to save time since the receiving part does not have to be rechecked against the specified Profile.
- Designer Awareness: Q-Checker anticipates and captures requirements of all downstream applications, even where they may not be evident to the designer. When operated already from the early beginning in the design process, Q-Checker will support and enhance cross-engineering as well as model reuse. The key to a successful implementation is the integration and adaptation to companies PLM processes.
Q-Checker: Interactive checking of CAD Data
Q-checker interactively checks the CAD designs i.e. parts, drawings, assemblies right in CATIA workbench and qualify immediately if the data meets the quality requirements as per company CAD standard or as mentioned in Q-checker profile. Q-checker can be run in a batch mode. There are more than 400 Data Quality checks already in-place in shipped licenses of Q-checker out of that 200+ checks have auto-healing function. Auto-healing function of Q-checker resolve the CAD concerns right automatically.
Figure 3: Q-Checker Interactive check user interface.
Q-Checker: Check Profile Creation
In any organisation, there can be many departments that have varying needs from the CAD designs. e.g. CAE team requires material specs, thickness, fixing locations etc, electrical team might not need these. So, Q-checker facilitates creating Check profiles individually for various departments in a organisation. Figure 4 showcases how to create check profiles in Q-checker and save according to the department name e.g. Electrical profile, Chassis profile, interior trims profile etc.
Fig 4: Q-Checker Profile creation UI.
We’ll discuss in detail some of the standard checks in the upcoming series.