Game Changing EOS Systems for Lifestyle and Consumer Goods Industry: Eyewear Applications
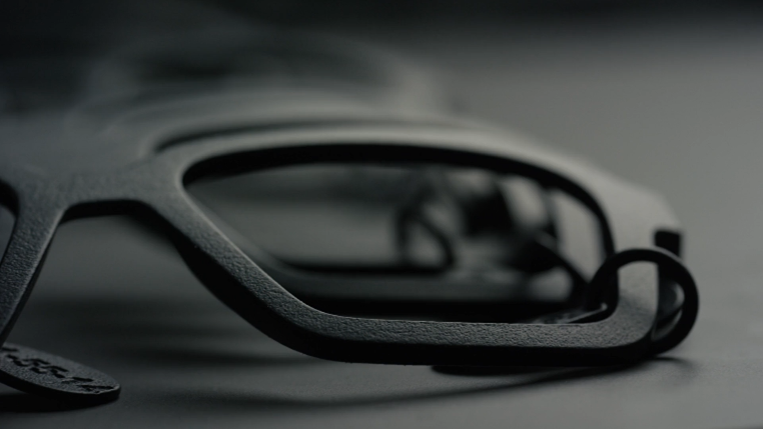
- Arun K. Kashyap
- December 26, 2024
Every person’s face is as unique as their personality, making custom eyewear not just a luxury but a necessity for optimal comfort and functionality. Traditional methods of manufacturing glasses frames are labor-intensive and costly, especially when tailored to individual needs. However, industrial 3D printing, particularly with EOS systems, has revolutionized this process, offering unmatched customization, efficiency, and sustainability.
The Power of EOS Technology in Eyewear Manufacturing
EOS additive manufacturing systems enable the production of both metal and plastic glass frames that meet the highest demands for design, functionality, and aesthetics. By combining cutting-edge technology with innovative materials like PA 2200, eyewear manufacturers can deliver frames that are not only lightweight and robust but also tailored to the unique facial features of each customer.
Fig.1: EOS system configuration for Eyewear production on demand
Key Advantages of EOS 3D Printing for Eyewear
- Virtually Limitless Customization: Glass frames can be designed to fit the exact contours of a customer’s face using 3D scanning technology.
- Enhanced Comfort: Lightweight and stable designs ensure maximum wearability.
- Sustainability: Reduced material waste and the ability to reuse leftover material make the process eco-friendly.
- Rapid Prototyping and Production: Quick turnaround times enable faster time-to-market and the ability to respond to customer demands swiftly.
- Cost-Efficiency: Additive manufacturing eliminates the need for minimum order quantities, allowing for the economical production of small batches or single units.
Success Story: 3x More Sustainable 3D Printed Eyewear by You Mawo
The innovative start-up You Mawo exemplifies the transformative potential of EOS 3D printing technology in eyewear. By leveraging the EOS P 396 system and PA 2200 material, You Mawo produces glasses frames that are:
- 30% Lighter than Acetate: The reduced weight enhances comfort without compromising durability.
- Tailored to Individual Needs: Frames are based on 3D scans of customers’ faces, ensuring a perfect fit.
- Environmentally Friendly: Additive manufacturing minimizes overproduction and shortens delivery paths, reducing the carbon footprint.
Fig. 2: Production of Customized and Personalized Eyewear using EOS SLS Process
The BRAGi Eyewear Revolution
Nanjing BRAGi Optical Technology Co., Ltd., has embraced EOS additive manufacturing for its business model. Using the FORMIGA P 110 Velocis system and PA 2200 material, BRAGi has created a streamlined process that includes:
- Scan-to-Print Workflow: Customers’ facial data is captured via 3D scanning, enabling precise customization.
- High-Quality Finishes: The material’s purity and surface quality allow for seamless post-processing and vibrant coloring.
- Hypoallergenic and Durable Frames: The glasses are not only lightweight and robust but also hypoallergenic, making them suitable for sensitive skin.
In just a few months, BRAGi produced over 30,000 custom glasses frames, expanding its market across Asia and receiving inquiries from Europe. This success underscores the scalability and global appeal of additive manufacturing in the eyewear industry.
Fig. 3: Scaled Finishing process for Production of Eyewear
The Strategic Advantage: P3 Next System for Eyewear Manufacturing
For eyewear manufacturers looking to scale their operations while maintaining precision and quality, the P3 Next system offers an unmatched commercial advantage. Its cutting-edge capabilities are tailored to meet the high demands of the eyewear industry, delivering both cost efficiency and superior performance.
Fig. 4: Improved throughput of efficient EOS P3 Next for Eyewear Application
Key Advantages of the P3 Next System
- Enhanced Productivity: Optimized workflow and innovative software boost machine productivity by 50% while reducing costs by 30%.
- Maximized Machine Availability: Achieve up to 90% machine availability with double material efficiency and an impressive 80% reusability rate.
- Advanced Software Solutions: Efficiently manage data preparation, production, and analytics for streamlined operations.
- Innovative Peripherals: Simplify workflows with state-of-the-art peripherals for part unpacking, finishing, material sieving, and mixing.
- Scalable and Cost-Effective: Enable scalable production with a minimal footprint, perfect for growing businesses.
- Precision-Driven Quality: Deliver consistent, high-quality results tailored to every application.
- Quick Time-to-Market: Leverage optimized and proven parameter sets to accelerate production timelines.
- Customizable Settings: Enhance both quality and performance with adjustable settings designed for specific needs.
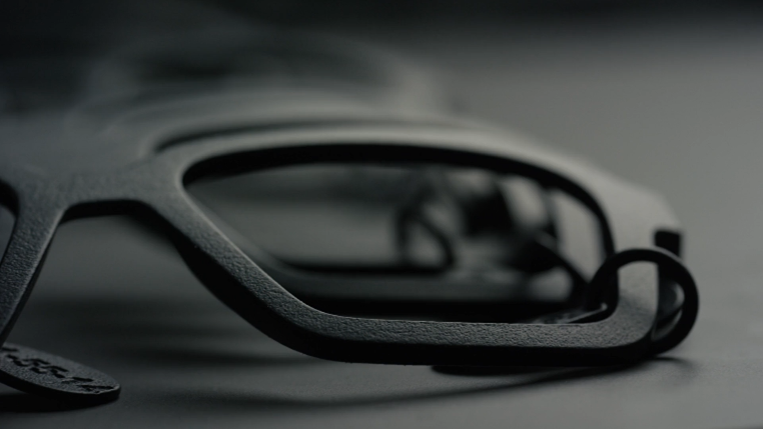
- Arun K. Kashyap
- December 26, 2024
Game Changing EOS Systems for Lifestyle and Consumer Goods Industry: Eyewear Applications
Every person’s face is as unique as their personality, making custom eyewear not just a luxury but a necessity for optimal comfort and functionality. Traditional methods of manufacturing glasses frames are labor-intensive and costly, especially when tailored to individual needs. However, industrial 3D printing, particularly with EOS systems, has revolutionized this process, offering unmatched customization, efficiency, and sustainability.
The Power of EOS Technology in Eyewear Manufacturing
EOS additive manufacturing systems enable the production of both metal and plastic glass frames that meet the highest demands for design, functionality, and aesthetics. By combining cutting-edge technology with innovative materials like PA 2200, eyewear manufacturers can deliver frames that are not only lightweight and robust but also tailored to the unique facial features of each customer.
Fig.1: EOS system configuration for Eyewear production on demand
Key Advantages of EOS 3D Printing for Eyewear
- Virtually Limitless Customization: Glass frames can be designed to fit the exact contours of a customer’s face using 3D scanning technology.
- Enhanced Comfort: Lightweight and stable designs ensure maximum wearability.
- Sustainability: Reduced material waste and the ability to reuse leftover material make the process eco-friendly.
- Rapid Prototyping and Production: Quick turnaround times enable faster time-to-market and the ability to respond to customer demands swiftly.
- Cost-Efficiency: Additive manufacturing eliminates the need for minimum order quantities, allowing for the economical production of small batches or single units.
Success Story: 3x More Sustainable 3D Printed Eyewear by You Mawo
The innovative start-up You Mawo exemplifies the transformative potential of EOS 3D printing technology in eyewear. By leveraging the EOS P 396 system and PA 2200 material, You Mawo produces glasses frames that are:
- 30% Lighter than Acetate: The reduced weight enhances comfort without compromising durability.
- Tailored to Individual Needs: Frames are based on 3D scans of customers’ faces, ensuring a perfect fit.
- Environmentally Friendly: Additive manufacturing minimizes overproduction and shortens delivery paths, reducing the carbon footprint.
Fig. 2: Production of Customized and Personalized Eyewear using EOS SLS Process
The BRAGi Eyewear Revolution
Nanjing BRAGi Optical Technology Co., Ltd., has embraced EOS additive manufacturing for its business model. Using the FORMIGA P 110 Velocis system and PA 2200 material, BRAGi has created a streamlined process that includes:
- Scan-to-Print Workflow: Customers’ facial data is captured via 3D scanning, enabling precise customization.
- High-Quality Finishes: The material’s purity and surface quality allow for seamless post-processing and vibrant coloring.
- Hypoallergenic and Durable Frames: The glasses are not only lightweight and robust but also hypoallergenic, making them suitable for sensitive skin.
In just a few months, BRAGi produced over 30,000 custom glasses frames, expanding its market across Asia and receiving inquiries from Europe. This success underscores the scalability and global appeal of additive manufacturing in the eyewear industry.
Fig. 3: Scaled Finishing process for Production of Eyewear
The Strategic Advantage: P3 Next System for Eyewear Manufacturing
For eyewear manufacturers looking to scale their operations while maintaining precision and quality, the P3 Next system offers an unmatched commercial advantage. Its cutting-edge capabilities are tailored to meet the high demands of the eyewear industry, delivering both cost efficiency and superior performance.
Fig. 4: Improved throughput of efficient EOS P3 Next for Eyewear Application
Key Advantages of the P3 Next System
- Enhanced Productivity: Optimized workflow and innovative software boost machine productivity by 50% while reducing costs by 30%.
- Maximized Machine Availability: Achieve up to 90% machine availability with double material efficiency and an impressive 80% reusability rate.
- Advanced Software Solutions: Efficiently manage data preparation, production, and analytics for streamlined operations.
- Innovative Peripherals: Simplify workflows with state-of-the-art peripherals for part unpacking, finishing, material sieving, and mixing.
- Scalable and Cost-Effective: Enable scalable production with a minimal footprint, perfect for growing businesses.
- Precision-Driven Quality: Deliver consistent, high-quality results tailored to every application.
- Quick Time-to-Market: Leverage optimized and proven parameter sets to accelerate production timelines.
- Customizable Settings: Enhance both quality and performance with adjustable settings designed for specific needs.