Space
Revolutionizing the space industry with designing, simulation, digital manufacturing, and additive manufacturing, offering an integrated approach to meet the unique demands of space projects. Advanced CAD and FEM mesh connectivity solutions streamline the design process, ensuring precision and efficiency. By leveraging cutting-edge technologies, seamless transitions from concept to production are enabled, enhancing the performance and reliability of space components.
Solutions for Space
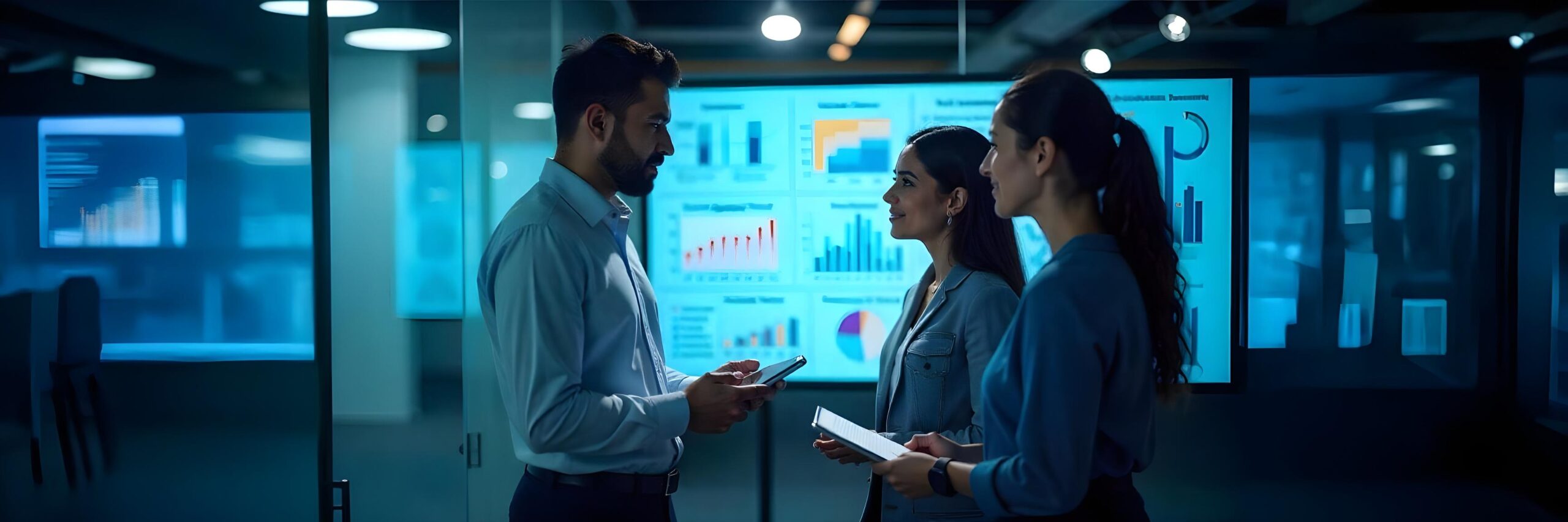
Ensuring Design Reliability for Consistent Performance
Design reliability is a key factor in ensuring that products perform as expected throughout their lifecycle, with minimal risk of failure. In industries ranging from automotive to aerospace, electronics to consumer goods, the ability to design products that can withstand real-world conditions while maintaining performance and durability is crucial.
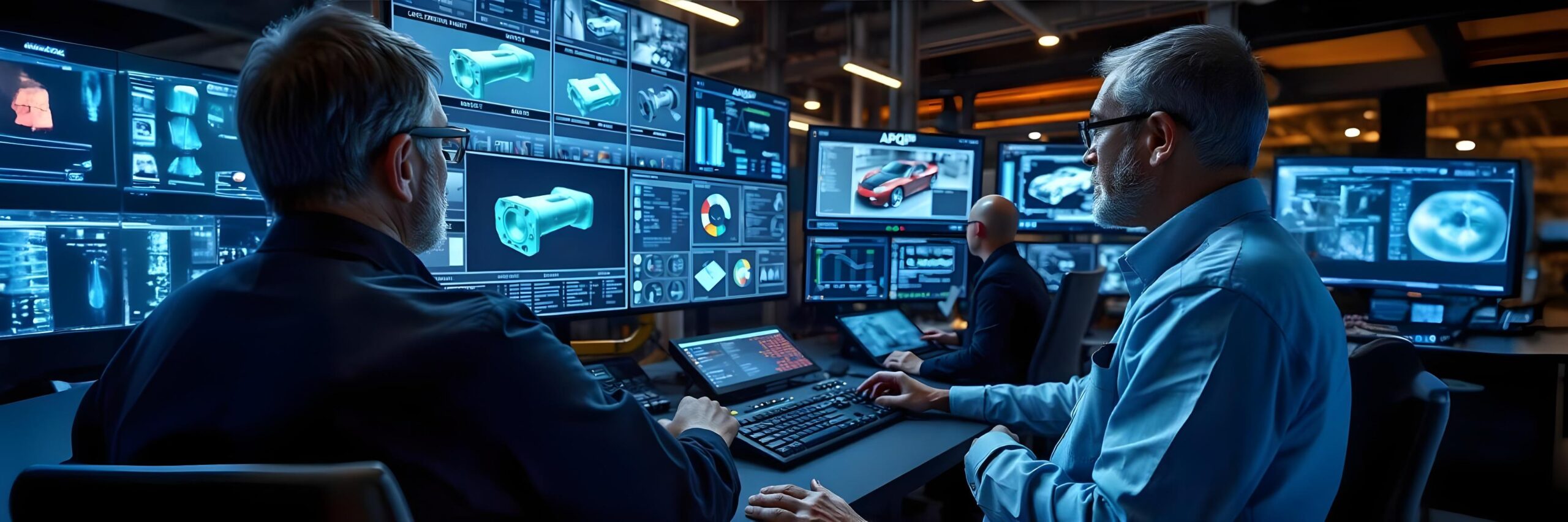
Real-Time Visibility in APQP & Process Adherence for Better Quality Control
Advanced Product Quality Planning (APQP) is a critical process in the automotive industry, originally developed to ensure products meet stringent OEM and consumer quality standards. Automotive suppliers often face challenges such as lack of real-time visibility, inconsistent process adherence, fragmented communication, and difficulties in managing the extensive data associated with product development.
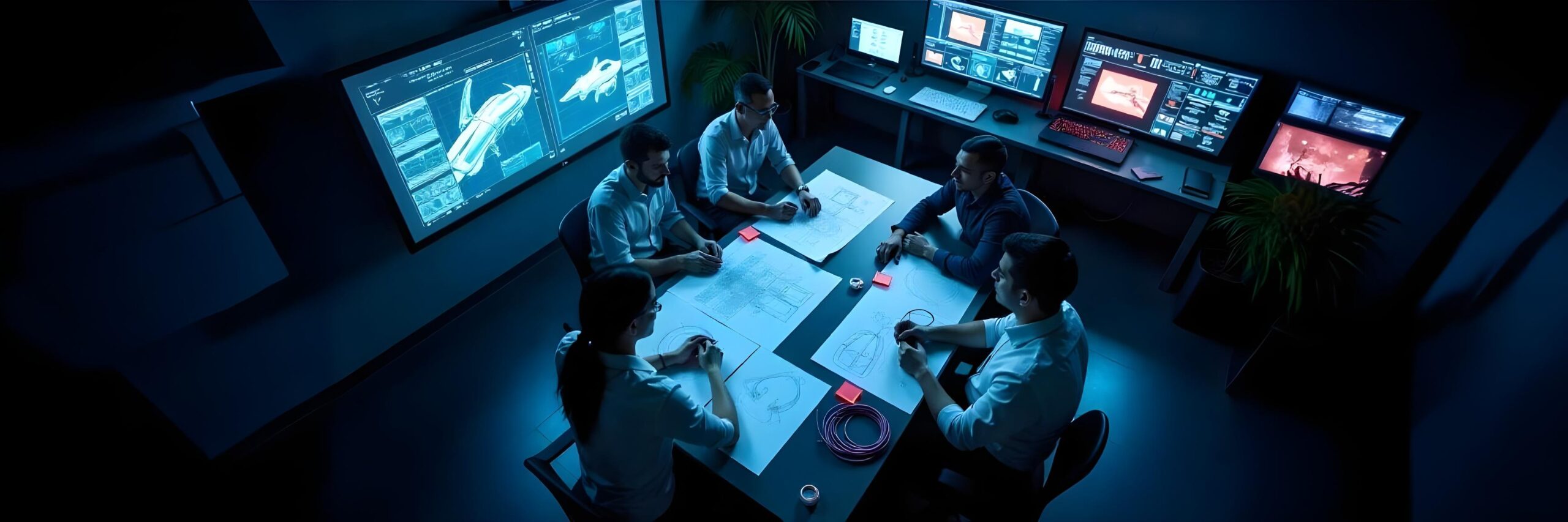
Advanced Composite Design for High-Performance Applications
Composite materials are increasingly being used across industries like automotive, aerospace, and defense due to their exceptional strength-to-weight ratio and ability to withstand harsh conditions. However, designing composites requires specialized tools to optimize material usage, ensure structural integrity, and meet performance standards. Advanced composite design involves not only sele

Optimizing Human Ergonomics for Safety and Comfort
Human ergonomics is essential for enhancing safety, comfort, and productivity in industries such as automotive, industrial equipment, and heavy machinery. Designing vehicles, machinery, and workspaces that are optimized for human factors reduces operator fatigue, improves posture, and prevents injuries. Optimizing ergonomics ensures operators can work efficiently and safely over extended periods.
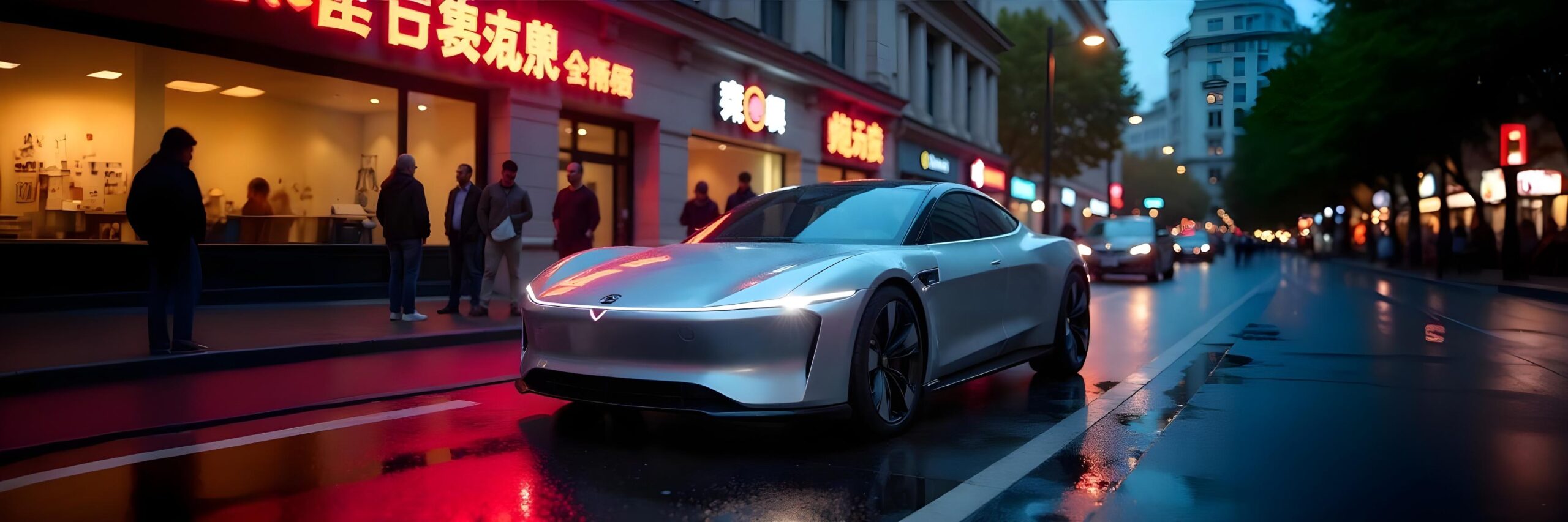
Lightweighting for Enhanced Performance and Efficiency
Lightweighting is a crucial strategy for improving performance, fuel efficiency, and overall sustainability across industries like automotive, drones, electric vehicles (EVs), and consumer goods. By reducing component weight, manufacturers can enhance product performance, increase energy efficiency, and reduce emissions, all while improving durability. Achieving lightweight designs requires advanced tools that can optimize strength, material usage, and durability.
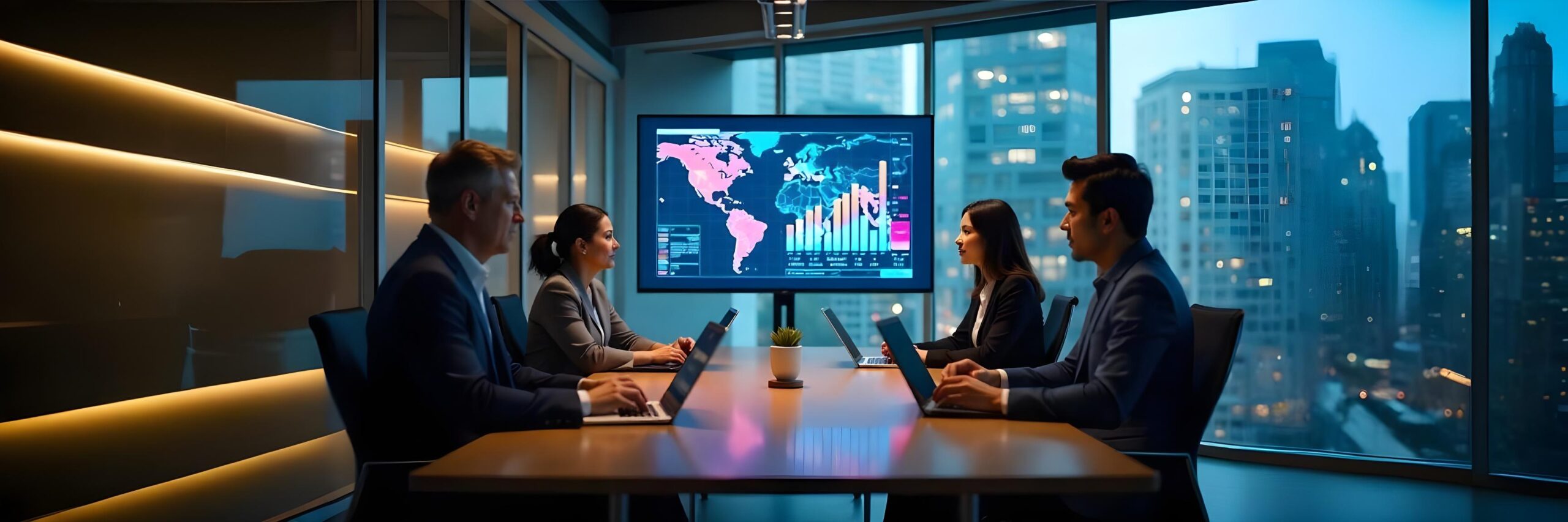
Streamlining Project Management with Data-Driven Insights and Collaboration
In today’s fast-paced environment, data-driven project management is essential for ensuring projects are delivered on time and within budget. By leveraging real-time data, teams can track progress, manage resources efficiently, and identify risks early. This approach enables quick decision-making, reduces delays, and optimizes project outcomes.
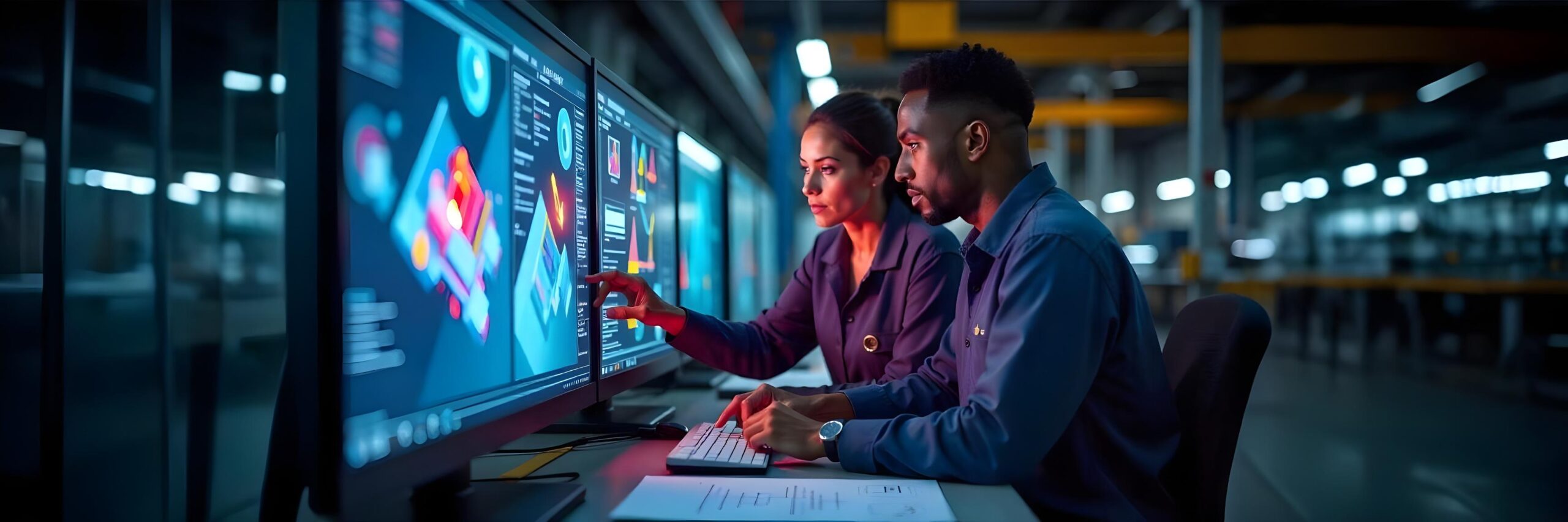
Enhancing Manufacturing Efficiency with Integrated Design Workflows
In today’s competitive manufacturing landscape, the integration between design and manufacturing workflows is critical for achieving higher efficiency, reduced costs, and faster time-to-market. When design and manufacturing processes are disconnected, errors, delays, and inefficiencies can arise, slowing down production and increasing operational costs. A seamless connection between these processes ensures that design intent is faithfully executed during production, improving product quality and reducing the need for rework.
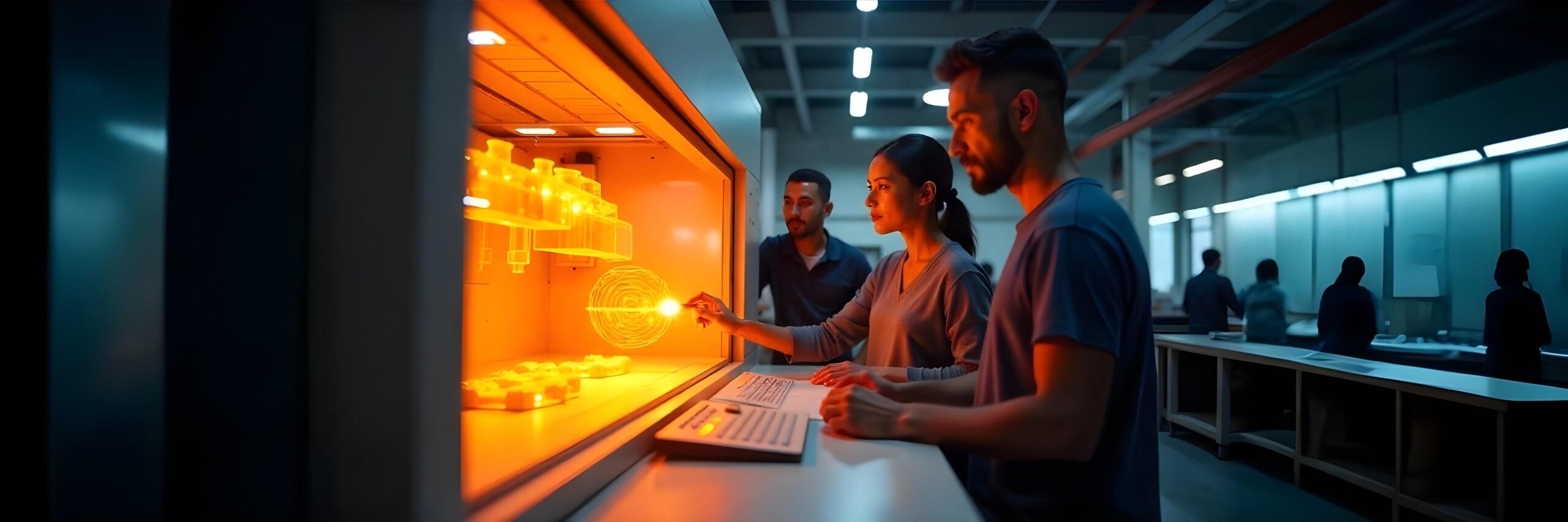
Optimized Design for Additive Manufacturing (DFAM)
Design for Additive Manufacturing (DFAM) transforms traditional design processes by enabling more efficient, innovative, and cost-effective solutions tailored for additive manufacturing technologies. This approach ensures that designs are optimized for 3D printing, making it possible to create complex geometries that were previously difficult or impossible to manufacture. By integrating advanced simulation, material selection, and process planning, DFAM accelerates product development cycles while maintaining or improving performance, reducing weight, and cutting costs.
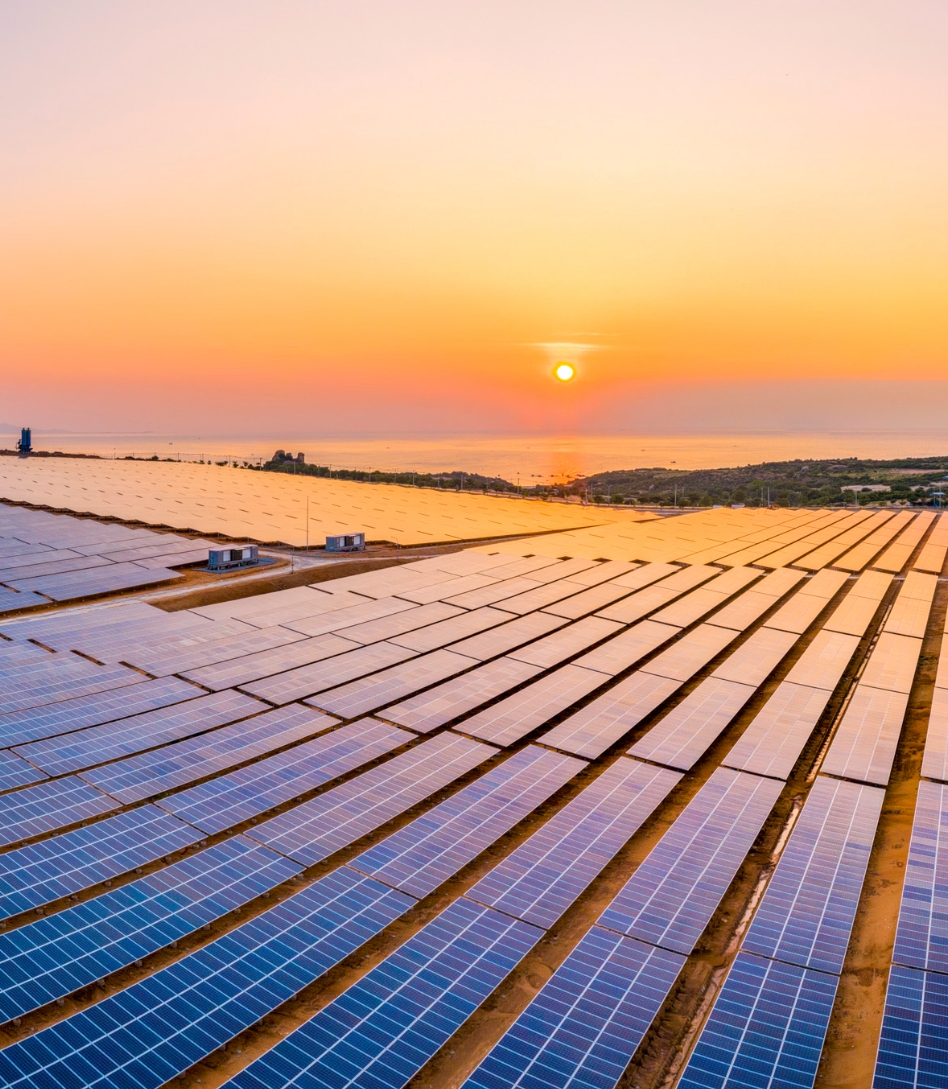
Products
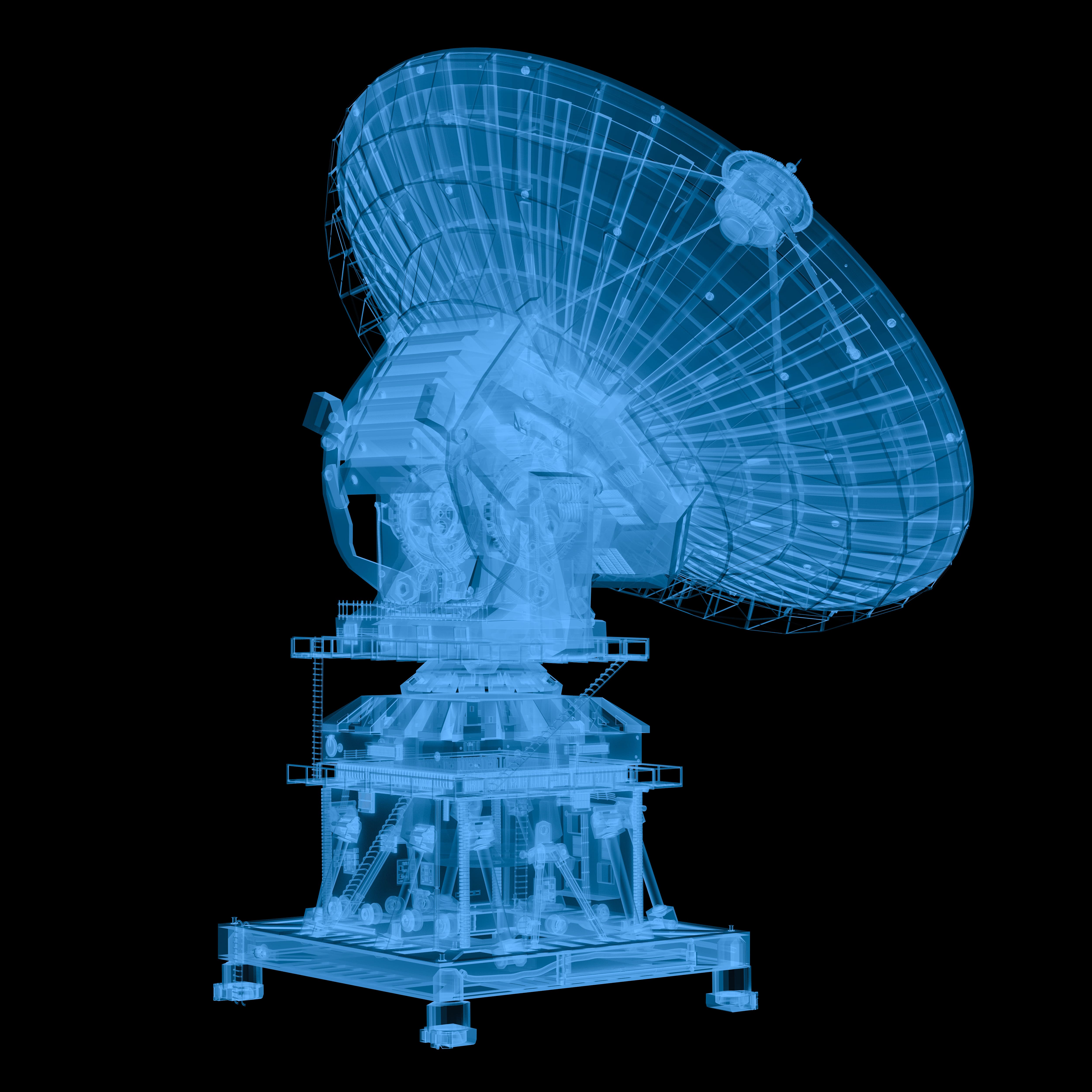
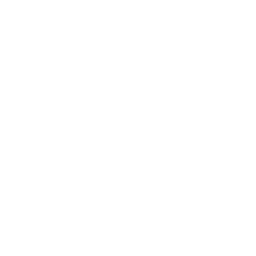
CATIA
Engineer lightweight, high-performance structures for satellites, launchers, and space infrastructure
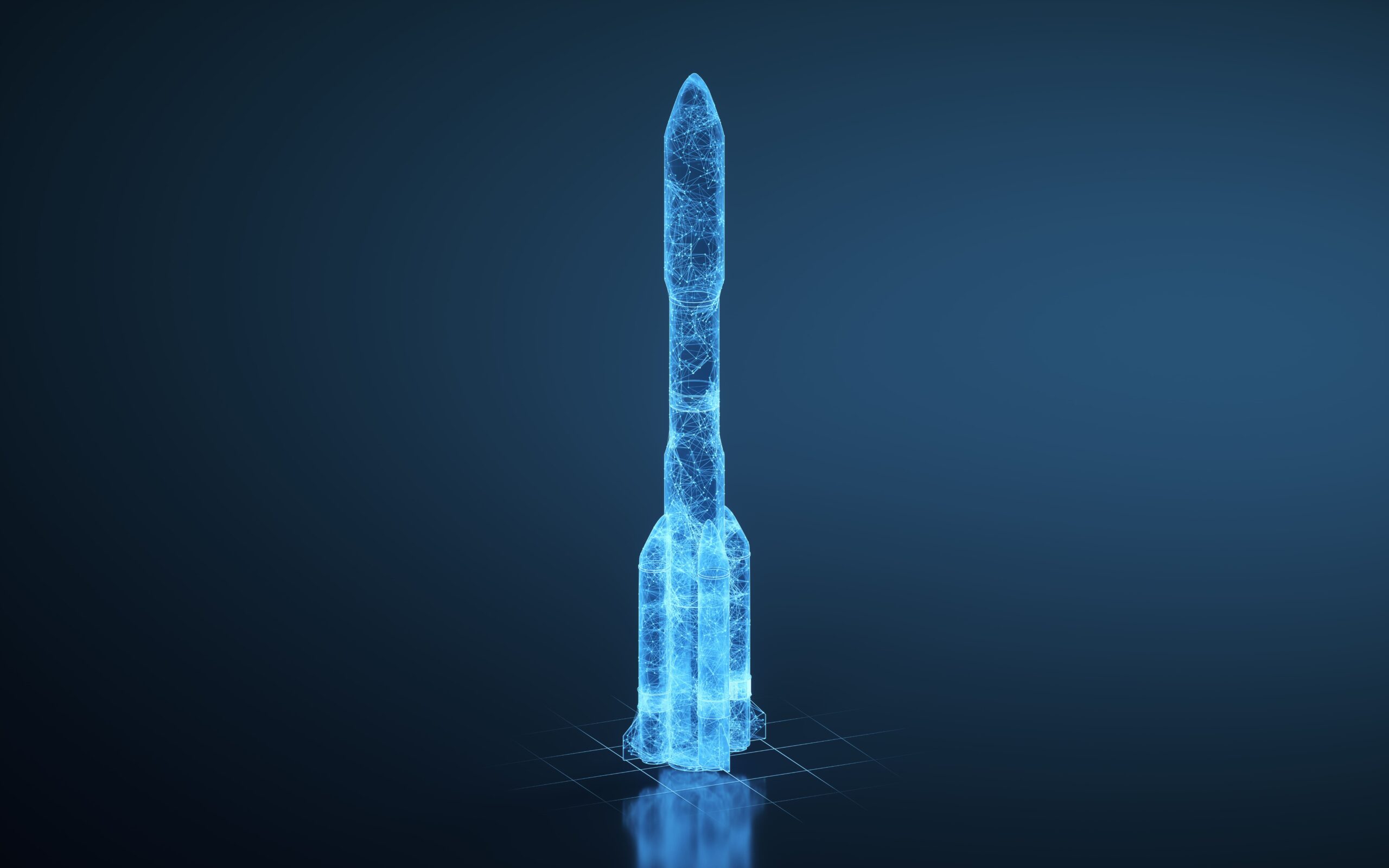
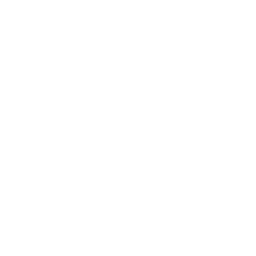
SIMULIA
Enhance durability and safety for all space applications with structural, thermal, and aerodynamic simulations
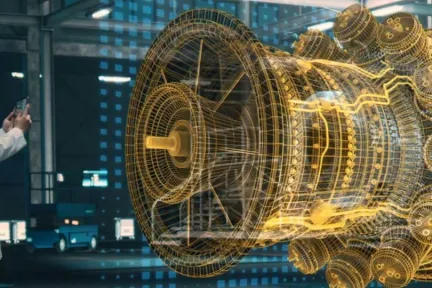
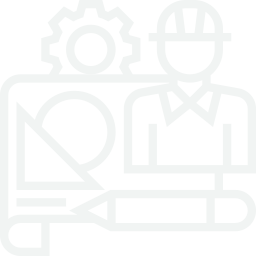
DELMIA
Streamline manufacturing of launch vehicles, satellites, and ground systems with digital precision
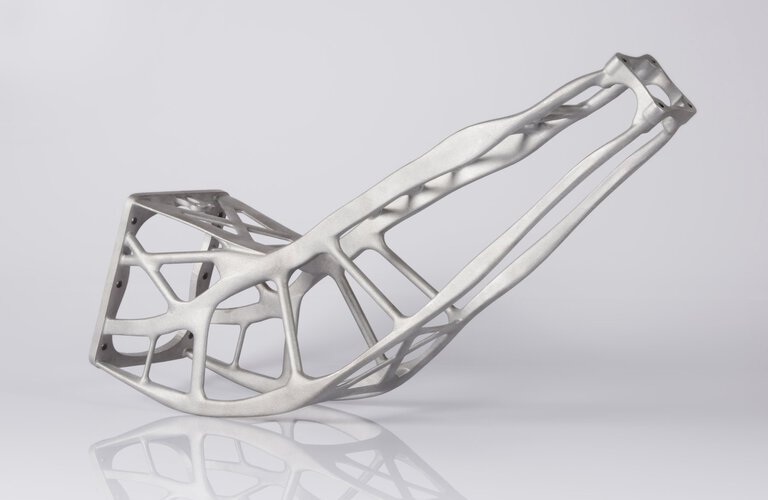
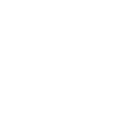
EOS 3D Printing
Accelerate space innovation with 3D-printed parts designed for extreme environments
Trends
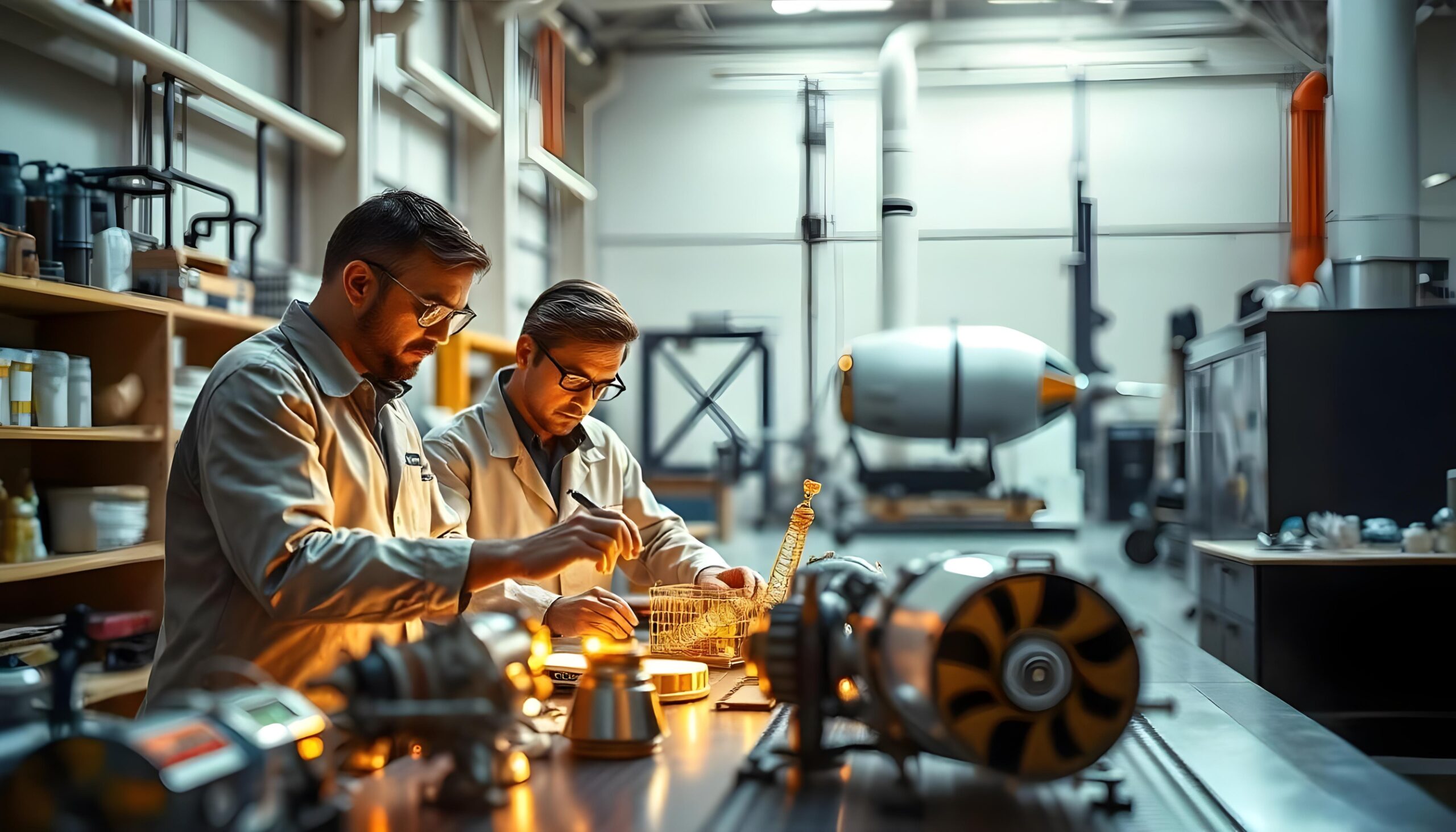
Increase Fuel Efficiency and Payload with Lightweighting in Space Exploration
In space exploration, maximizing fuel efficiency and payload capacity is critical to mission success. One of the most effective ways to achieve this is through lightweighting—reducing the weight of spacecraft components while maintaining their strength and durability. CATIA, Dassault Systèmes' advanced design software, allows engineers to create optimized, lightweight structures with precise geometry, while EOS, a leader in additive manufacturing, enables the production of these parts using high-performance materials through 3D printing. By combining CATIA’s powerful design capabilities with EOS’s additive manufacturing technology, space agencies and manufacturers can produce lightweight yet strong components, significantly reducing fuel consumption and increasing payload capacity. This approach enhances the efficiency and sustainability of space exploration missions, enabling more cost-effective and successful space programs.
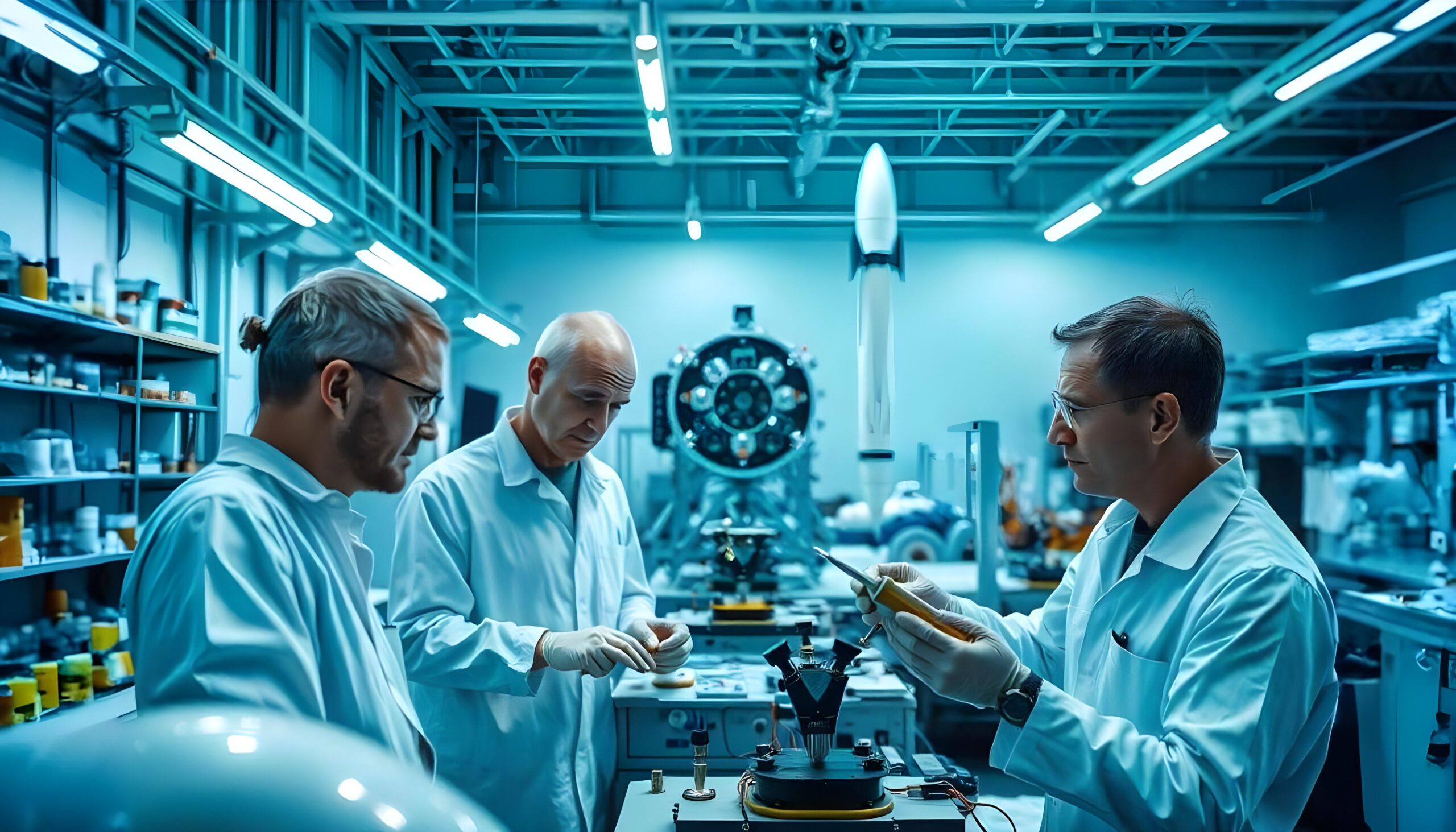
Collaborative Mechatronics Engineering for Space Systems
In the space industry, developing complex space systems requires seamless collaboration across multiple engineering disciplines, particularly in mechatronics, which combines mechanical, electrical, and software systems. The integration of these systems must be precise to ensure the reliability and performance of spacecraft, satellites, and other space technologies. ENOVIA, a leading product lifecycle management (PLM) solution, fosters this collaboration by providing a unified platform for engineers to manage the design, simulation, and production processes of mechatronic systems. With ENOVIA, teams from different domains can work together in real-time, ensuring alignment, reducing errors, and streamlining workflows. This collaborative approach accelerates development, enhances innovation, and ensures that space systems are engineered for maximum efficiency, safety, and performance.
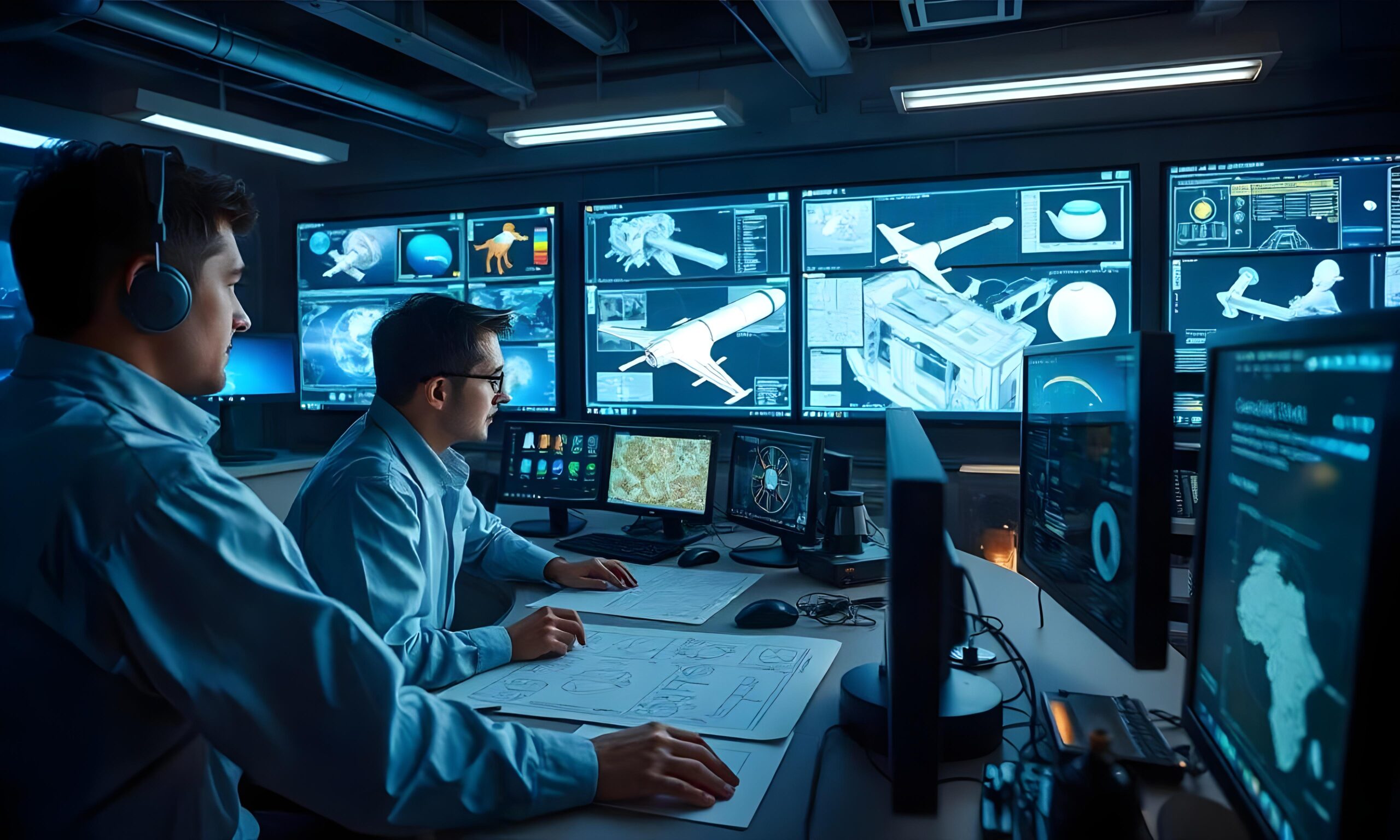
Enhance Space Systems Design with Advanced Systems Engineering Solutions
Designing space systems requires the integration of complex subsystems, including propulsion, avionics, power, and communication, all of which must function seamlessly together in extreme environments. CATIA, Dassault Systèmes’ advanced systems engineering software, enables engineers to create, simulate, and optimize these intricate systems with precision. By offering powerful tools for multi-disciplinary design, simulation, and collaboration, CATIA ensures that each component of the space system is efficiently integrated and performs optimally. With CATIA, space agencies and manufacturers can streamline the development process, reduce risk, and improve the performance and reliability of space systems, ensuring mission success in challenging conditions.
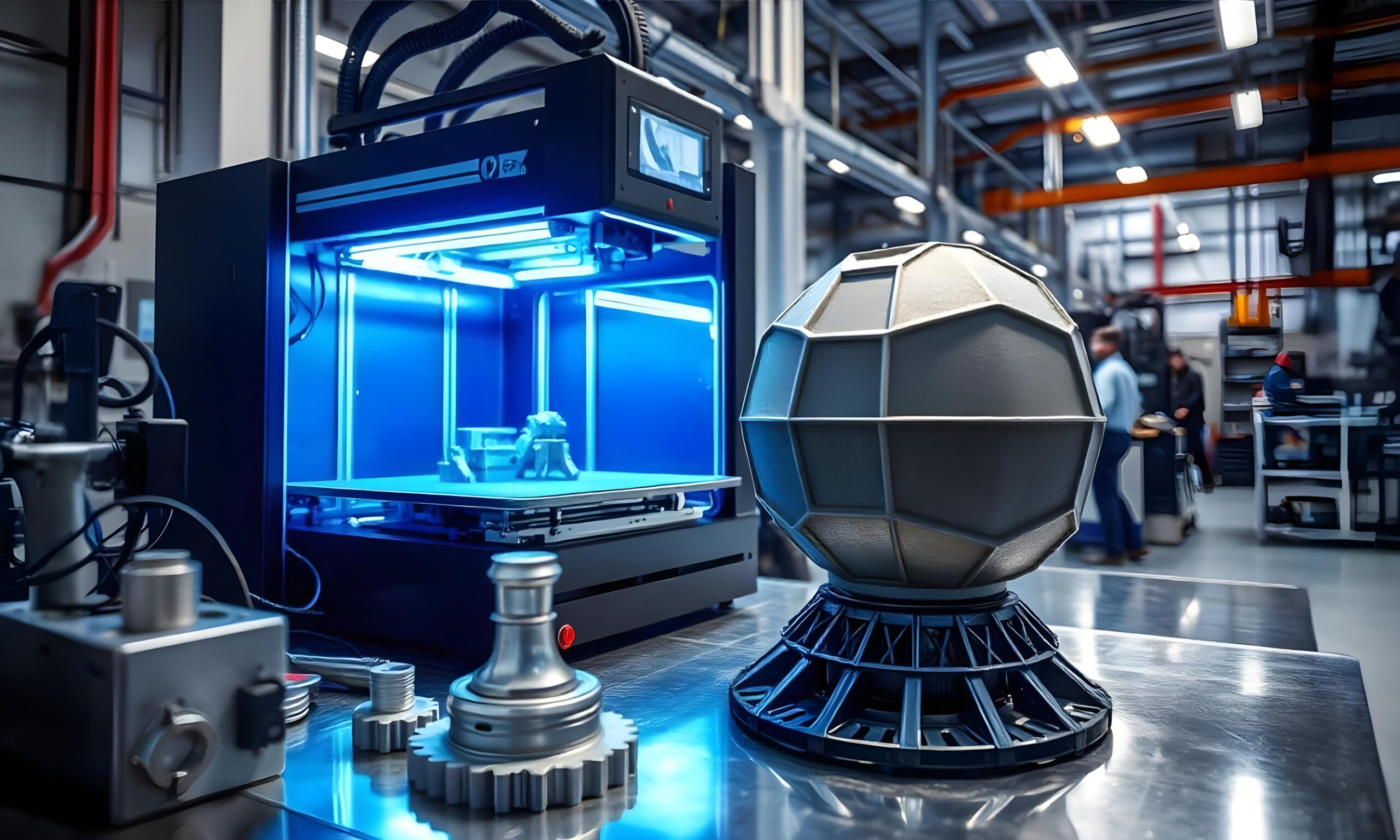
Advancing Spacecraft and Satellite Development with Additive Manufacturing
In the development of spacecraft and satellites, the demand for lightweight, high-performance components is crucial to ensuring mission success and reducing costs. Additive manufacturing (AM) offers a transformative solution by enabling the creation of complex, optimized parts with reduced weight and enhanced functionality.
Latest Blog Posts
Discover our most recent posts across Aerospace and Defence Industry.
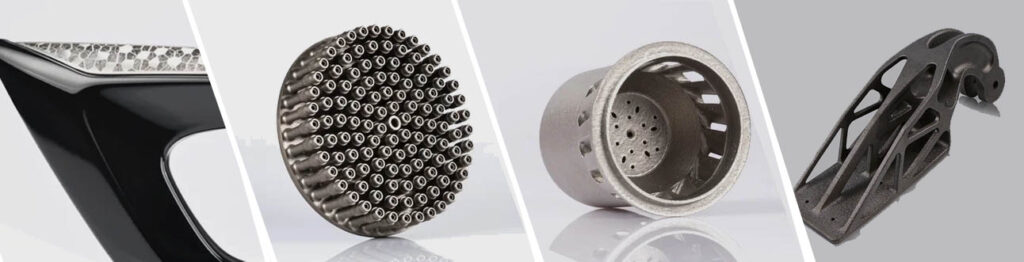
Overview on DMLS Process for 3D Printing and its Applications in Space Industry
Additive Manufacturing Additive manufacturing is a specific 3D printing process where parts are built layer by layer by depositing material according to digital 3D design data. For…