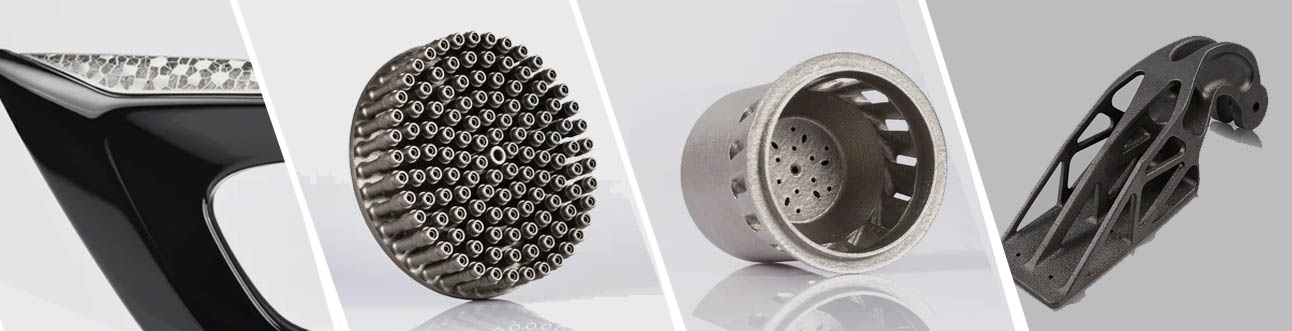
Overview on DMLS Process for 3D Printing and its Applications in Space Industry
Additive Manufacturing
Additive manufacturing is a specific 3D printing process where parts are built layer by layer by depositing material according to digital 3D design data. For example, instead of milling a workpiece from a solid block, additive manufacturing builds the part up layer by layer from raw material supplied as a fine powder. This technique is known as Powder Bed Fusion.
Powder Bed Fusion (PBF)
Powder Bed Fusion (PBF) is a laser or electron-based additive manufacturing technique. This is categorized based on the different working systems such as Selective Laser Sintering (SLS), Selective Laser Melting (SLM), Electron Beam Melting (EBM) and Direct Metal Laser Sintering (DMLS). In PBF, DMLS is recognized well in the industrial sectors such as aerospace, defence, automobile, tooling, space launch vehicles, biomedical, electric, and marine. The advantage of the DMLS process is that end components, with freedom of design, higher complexity, tailor-made customization, material reuseable and weighting reduction (lightweight structure) can be manufactured without any change in performance.
Direct Metal Laser Solidification:
DMLS follows the principle of “Direkt Metall Laser Schmelzen” (Direct Metal Laser Melting in English). It is a proven Laser – PBF (LPBF) technology and is now the standard in metal 3D printing. DMLS operates with the principle of high-intensity ytterbium laser beam as an energy source. The laser beam melts the selective powder particles into liquid stages from the melt-pool and gets cured rapidly for the required layer known as a layer thickness. In DMLS, an inert atmosphere (argon or nitrogen) is maintained in the working chamber. Inert gas with high purity has to be used to keep oxygen at the correct level and decrease flammability in the presence of hydrogen. DMLS process is capable producing complex and lightweight structures. The DMLS workflow is displayed below:
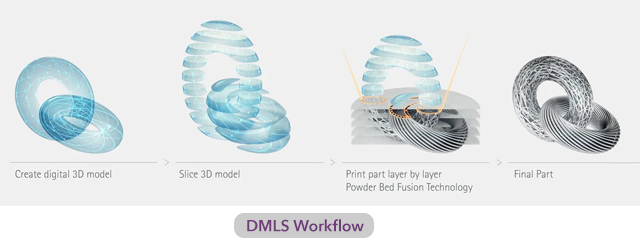
Feedstock Material widely used in DMLS:
- Stainless Steel – StainlessSteel GP1, StainlessSteel PH, CaseHardening Steel
- NickelAlloy – IN718, IN625, HX
- Cobalt Chrome – CobaltChrome SP2
- Titanium Ti64
- Aluminium AlSi10Mg
- Copper – Pure Cu & CuCrZr
Additive Manufacturing in Space Industry
In space sector, spacecraft and satellites are always looking for new innovations and cutting edge technologies. An increasing number of new start-up companies are entering the space sector. With the knowledge of AM process, they can produce their required designs which are complex while remaining cost-efficient overall.
Benefits of Additive Manufacturing in Space Industry
- Design for Additive Manufacturing:
For space launch vehicles, the parts and structures need to be light-weight without affecting the performance. In addition, the functionality of parts can be completely redesigned based on Design for Additive Manufacturing (DFAM) process. For example, multiple parts can be consolidated into a single all-in-one design.
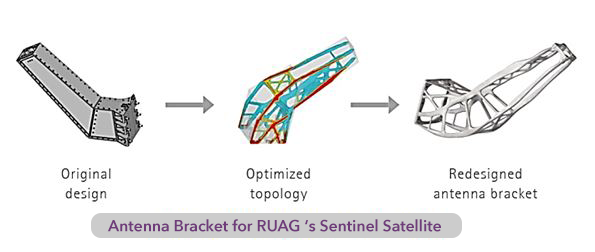
Currently, many space components and satellite brackets are manufactured through DMLS process to launch small to medium-sized payloads into space more efficiently than ever before. The results include novel and innovative rocket designs and the world’s largest rocket engine to ever be manufactured additively in a single piece. The engine is based on a standard rocket design but is extended with internal ribs for optimal cooling.
- Speed and Productivity
In the rapidly growing market of commercial space applications, DMLS processability to manufacture prototypes and small series productions plays a significant role with a lesser lead time and a cost-effective process. There are often extreme customer-specific requirements, particularly on aerospace parts, which perfectly matches the possibilities offered by additive manufacturing.
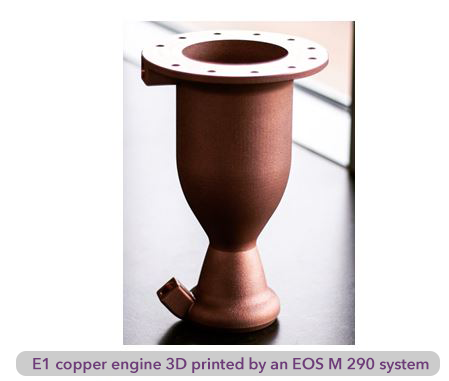
EOS 3D Printed Combustion Chamber for Rocket Engine
Over the past few years, the space sector has blossomed rapidly with many diverse start-ups specializing in development of end components. One of the start-ups based out of US is employing AM process on its mission to orbit. They successfully constructed and tested the new design quickly and cost-efficiently based on their development. The difficulties included the size of the build space and the material properties. AMCM, a company in the EOS group that offers specialized machines tailored to customer requirements, accepted this challenge.
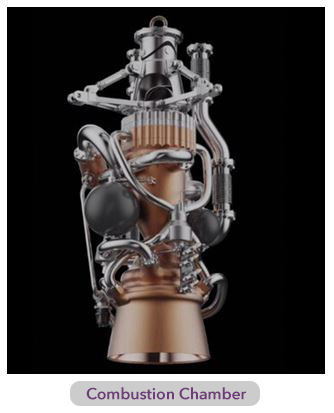
The combustion chamber, printed with the copper alloy on AMCM’s M4K machines, is the largest single-piece combustion chamber for liquid rocket engines in the world.
The chamber is 86 cm (34 in) high, with an outlet nozzle diameter of 41 cm (16 in).
Manufacturing challenges are addressed by additive manufacturing. This type of part requires higher investment in custom machines. Now, they are utilising the DMLS process to print the combustion chamber, nozzle and neck combined into a single piece.
DMLS technique and its various applications are recognized well in industrial sectors for providing the solutions with new design and manufacturing processes to produce complex parts. DMLS techniques also offer unique process parameter optimization to produce high-quality parts rapidly with intuitive mechanical properties and dimensional accuracy.
Image courtesy: EOS
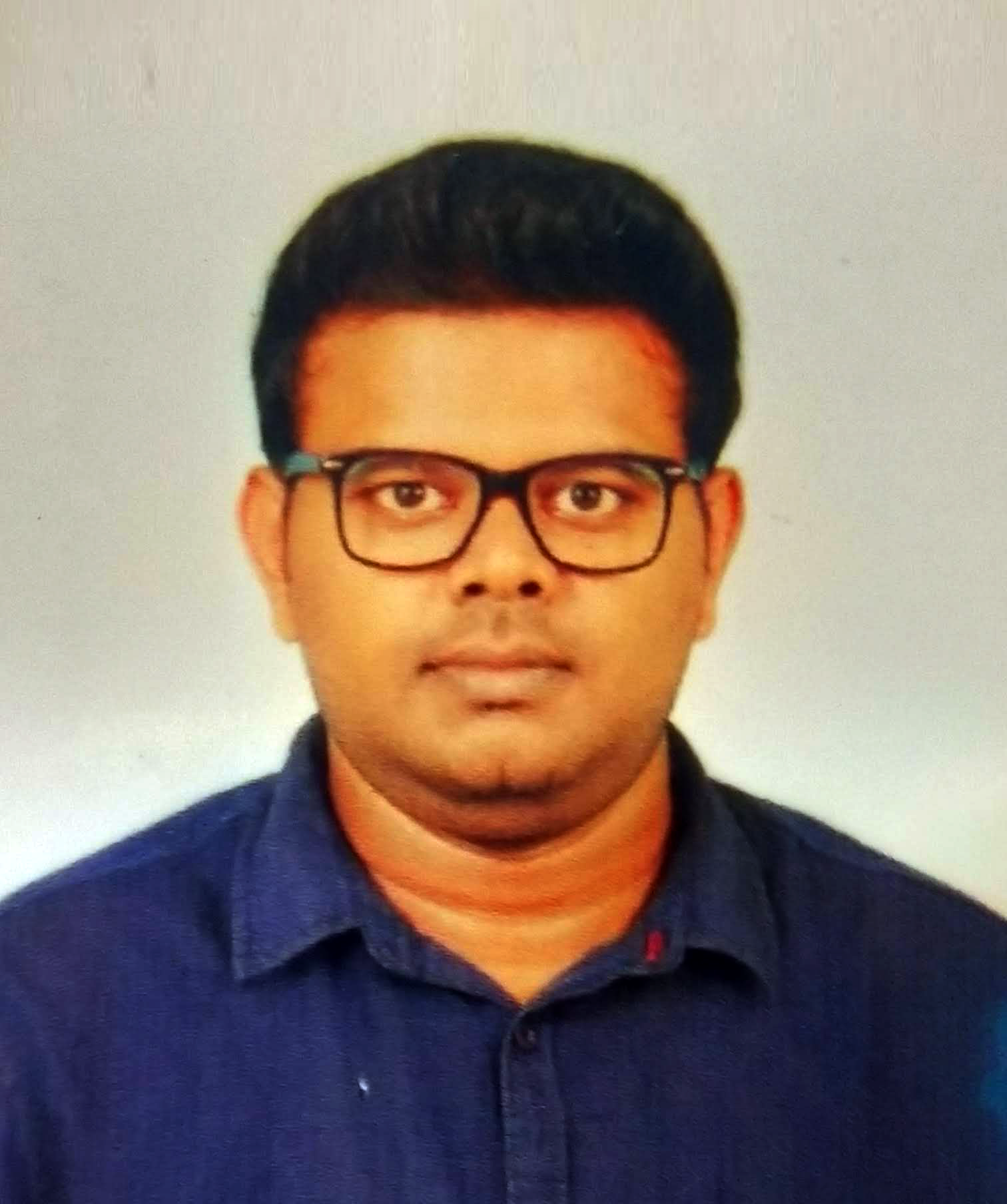
Mugeshwaran started his career as Junior Research Fellow. He has worked in diverse Metal and Polymer Additive Manufacturing organisations for three years. He is currently working as an application engineer at EDS Technologies for Additive Manufacturing. He has a good experience in Design for Additive Manufacturing (DFAM) across various industries like Aerospace, Life Sciences, Tooling and General Engineering.