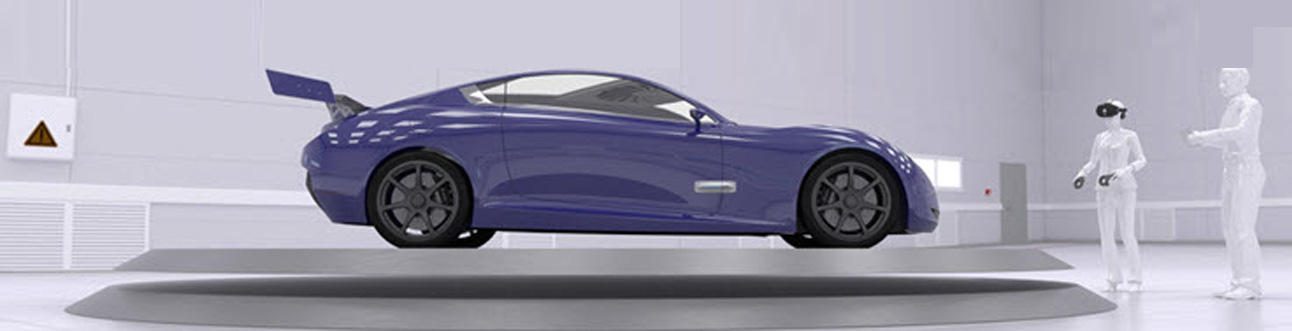
How companies optimize their Design, Engineering and Manufacturing Processes?
Organizations are adopting Lightweight Engineering solutions to optimize their design, engineering and manufacturing processes. R&D departments in the Automotive and Aerospace sector is increasingly considering ways to adopt Lightweight Engineering solution to develop the new product designs.
There are multiple methods to optimize the weight, shape and material selection of parts and assembly. However, Lightweight Engineering is much more than this. Lightweight Engineering is the optimization of design, engineering and manufacturing processes which helps to create and evaluate new types of concepts and techniques that will make better lighter products.
There are multiple challenges which are faced while designing a part for Lightweight Engineering. Some of the challenges are listed below:
- How to optimize the weight and shape of the design and further simulate and test virtually considering the entire Vehicle or Aircraft Design?
- How to optimize fastening in complex assemblies?
- How to achieve paperless engineering and manufacturing?
- How to optimize the process for composites from design to engineering to manufacturing stages?
- How to achieve a complex sheet metal part design right the first time in Aerospace and Automotive sectors?
- How to manage weight and balance workflow to achieve the KPI?
To address the above challenges, there are multiple processes and digital validation solutions which traditionally work in silos. However, a single solution which can carry design, engineering and manufacturing processes with the same digital thread without any data loss is desirable and preferred as well.
CATIA for Lightweight Engineering solution addresses the above challenges through:
- Cognitive Augmented Design with respect to Additive Manufacturing with best trade-off analysis approach
- Simulation Driven Design for Digital Continuity with SFE concept
- Reverse Engineering Processes with methodology and approach – from scan of “as built” or FEA deformation prediction results
- Fastener analysis and review in earlier stages for complex Assemblies
- Fully optimized process from design to simulation to manufacturing for composites
- First time right approach for complex sheet metal parts by considering manufacturing constraints
- Quicker design innovations in Mold Tool Designs
- Predicting the change management with best impact analysis approach
- Predicting mass distribution to balance weight in the earlier stages for large assemblies
- Increasing the quality of manufactured products with minimal tolerancing and drawing interpretation errors by 100% Product Manufacturing Information in 3D for accurate & annotated geometric definition
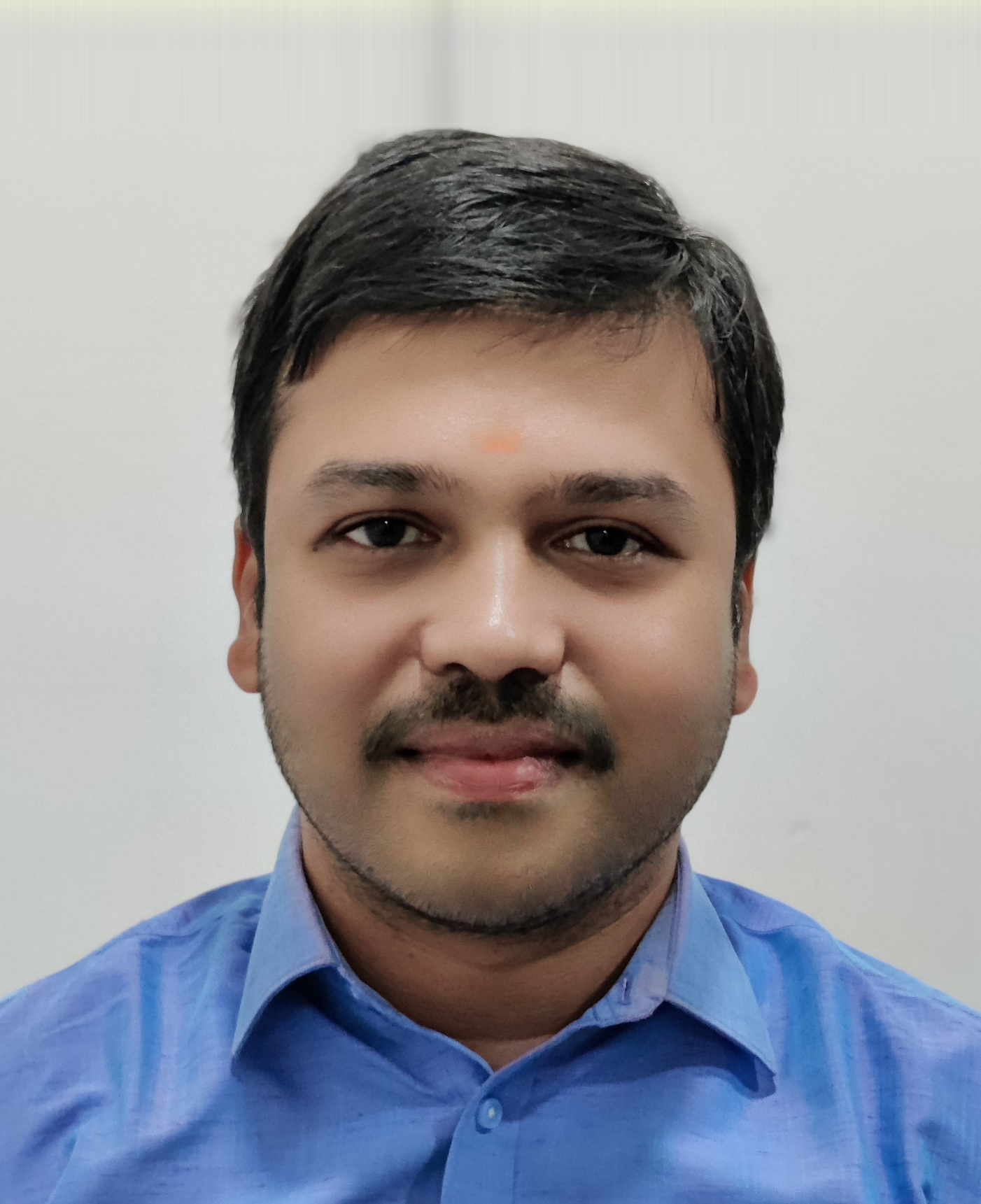
Mr. Lakshmi Narayana started his career as Design Engineer. He has more than 12 years of experience in design, manufacturing, solution consulting and technical support in CAD/CAM domain. He is currently working at EDS Technologies as Senior Solution Consultant PLM CoE with a good exposure to design and manufacturing (machining) projects especially in Automotive domain. He has certification from Dassault Systèmes.